PS-104
2011/04/30 created
2022/05/27 updated
Analog Disc Player
Features | Direct-drive turntable, S-shaped static balance tonearm, MC cartridge,
Layered plywood board cabinet (Baumkuchen cabinet) |
---|---|
Outline specifications | Turntable speed: 33 1/3, 45rpm. Wow and flutter: <0.025%. Output voltage: 0.3mV. Frequency range: 15Hz-50kHz. Load impedance: 100ohm. |
Dimensions | 530mm(W) x 230mm(H) x 430mm(D). Weight: 19.3kg. |
Cost | Initial cost: approx. 70,000 JPY (estimation). Replacement styluses: approx. 320,000 JPY. Replace ment cartridge: approx. 68,000 JPY. |
History | Built in 1982. The cartrige (Satin M-14LE) was replaced with Grace F-14
in 1982. Magnetic insulators were tried out in 2012, but they were judged
to be invalid. F-14 was replaced with Ortofon 2M Red in 2012. 2M Red was
replaced with audio-tachnica AT33PTG/II in 2014. Currently out of use. |
The following contents were reprinted from the page of PS-104 on my previous homepage 'Tonochi's Audio Room'. The page describes my activities concerning this analog disc player from 1982 through 2014.
Concept
I wanted a player with high price performance ratio, high stability and a long life. I wasn't inclined to select a cartridge for low stylus tracking force and a light-weight tonearm, which were popular in '70s. I was going to select a heavy turntable driven by a strong motor, though it was servo controlled.
Key parts
The key parts I purchased for PS-104 are as shown below:
Category | Manufacturer | Model # | List price | Purchase price |
---|---|---|---|---|
Turntable | Sony | TTS-8000 | 80,000 JPY | 19,800 JPY |
Tonearm | Grace | G-1040 | 28,000 JPY | 16,000 JPY |
Cartridge | Satin Grace |
M-14LE F-14 prototype |
16,400 JPY -- |
(forgotten) (forgotten) |
Insulator | DENON | AF-10 | 5,000 JPY | (forgotten) |
Though the purchase prices of the turntable and the tonearm are a lot cheaper than the list prices, they were not secondhand nor ones displayed at a storefront, but they were brand-new ones that hadn't been unpacked. I began purchasing the parts in fall 1981. At that time, there was a feeling that analog discs might have no future in hi-fi circles because the advent of DADs (DAD: generic name for digital audio discs such as CD or AHD) was just around the corner. Parts for analog players were being dumped at Akihabara district. That's why I could buy these parts at such low prices.
The reasons why I selected those parts are as follows:
Turntable
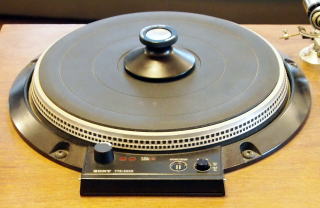
It was the discounted price that made me select TTS-8000. I bought it without
hesitation at a shop at Akihabara, when I happened to find it sold at about
20,000 JPY, one-fourth of the list price, though it was the top-of-the-line
model of SONY's turntables.
TTS-8000 is high-performance just as expected of the top-of-the-line. It
is a direct drive turntable, which was mainstream those days. Wow flutter
is as low as 0.025% with the servo control using X'tal oscillator (it was
called quartz-lock or X'tal-lock then). In spite of the employment of the
servo control, the turntable is so heavy that it can achieve low wow flutter
without the X'tal lock.
The rubber mat contains gel in it to prevent vibration from reaching the
disc on it.
The photo on the right shows a disc stabilizer is on the center of the
turntable. It was not an accessory of TTS-8000. I introduce it in the section
'My Own Review'.
Tonearm
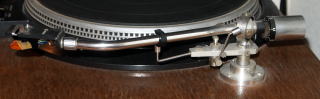
GRACE (Shinagawa Musen Co., Ltd.) is a Japanese pickup products corporation.
Though their major products were middle-grade ones, they had superb technology
and supplied products to broadcasters and record manufacturers as well.
They had collaborated with NHK STRL (Science & Technical Research Laboratories
of Japan Broadcasting Corporation) to develop some products.
GRACE had a hit product called G-545, a static balanced tonearm that employed
their proprietary gyro gimbal support technology. It was well-known for
almost no aged deterioration. The price was reasonable (around 15,000 JPY).
G-1040 is the successor of G-545.
G-1040 is a simple tonearm and its design sticks with the basics. It has
only basic features unlike other high-grade tonearms, and its basic performance
is superb. I knew the high reliability of GRACE products, so I bought G-1040
without hesitation, when I found it sold at the discounted price. Soon
after that, its list price was raised to 41,000 JPY. I was lucky to obtain
it at the low price.
Warranty period was not specified for any GRACE product and no warranty
document was attached. This doesn't mean GRACE didn't guarantee their products.
On the contrary, they would guarantee their products as long as GRACE existed.
This is a sign of their confidence in quality and reliability of their
products.
Cartridge
At that time, I owned three cartridges; SATIN M-14LE, SHURE M-75ED/II and
ELAC 355E. Till then, I had been using each of them according to my mood
or the genre of music to play. For PS-104, I changed my way. I decided
to select only one cartridge and to tune the other components to bring
out its real performance.
Of these three cartridges, my absolute favorite was SATIN M-14LE. It was
a high output MC cartridge. Its special feature was user-replaceable stylus.
As long as I know, it is the only MC cartridge having replaceable stylus.
It sounded so clearly and dynamically. In addition, it was designed user
friendly and its price was reasonable. I even regarded it as a Japanese-made
excellent audio product we Japanese could be proud of. I didn't hesitate
to choose it for PS-104.
However, it was a short period during which I used M-14LE. I received a
direct mail (DM) from GRACE that advertised they would distribute the prototype
of F-14 at a low price since I registered G-1040 just after I bought it.
F-14 is the export version of F-9, which is the higher-grade model of the
major hit cartridge F-8. I knew the excellent sound quality of GRACE cartridges
very well, because I went to 'GRACE Concert' (a record concert held by
GRACE; it was held at Ochanomizu district in Tokyo) every year from my
high school age to my mid-20s. I purchased the prototype. It was difficult
to judge which was better in sound quality, M-14LE or F-14. I chose F-14
because of its high compatibility with the tonearm G-1040 and its wide
variation of replacement styli.
This is the beginning of the long-term relationship between GRACE and me.
Since then, I have been receiving DMs periodically, and have bought many
GRACE products directly from it. Now I have an acquaintance with Mr. Akira
Asakura, the founder and CEO of Shinagawa Musen. I contact him via mail
or telephone from time to time.
I would like to keep the M-14LE as a spare cartridge, but I sold it to
a friend of mine who begged me to sell it.
![]() | |
GRACE F-14 prototype with elliptical stylus and ruby cantilever There's no logotype 'F-14'. |
GRACE F-14 prototype with elliptical stylus and ruby cantilever Serial # is handwritten. |
Insulator
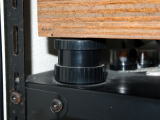
In the early '80s, many expensive insulators were available. Though DENON
AF-10 was a budget insulator, I supposed it was a good one by looking at
and touching it. I selected it.
I remember it is made of more than on kind of rubber and absorbs wide range
of vibration. It is user friendly because it can be fixed to the cabinet
with screws and adjust the height easily.
I don't know its exact purchase price now, because I didn't jotted it down.
But I remember I bought it at a discounted price too. In spite of the low
price, it excels in both performance and durability. I have been using
it for 32 years as of August 2014, yet it still maintains high elasticity
and absorbs vibration very well.
Construction of the Cabinet
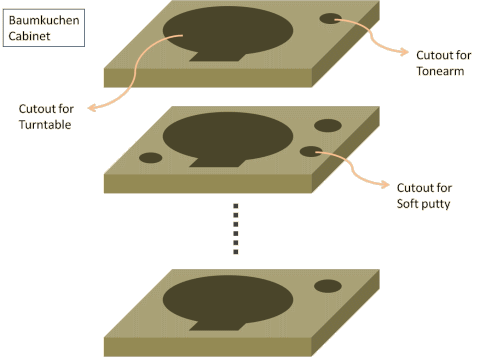
I employed so called Baumkuchen Cabinet invented by late audio reviewer Tetsuo Nagaoka. It is built by stacking multiple lauan plywood boards. Its four sides look like a baumkuchen (German cake), so Testuo Nagaoka named it Baumkuchen Cabinet. By employing this construction, a vibration proof cabinet can be built easily and cheaply.
The specified cutouts for the turntable and the tonearm of which are made in the top board. A little larger cutouts are made in the other boards.
I wouldn't be satisfied with the cabinet if it had been a 100% copy of Nagaoka's design. I added one more feature that was my own idea. I drilled some holes in one of the boards between the top and bottom, and filled them with soft putty to absorb vibration.
A set of the insulators are screwed to the bottom board.
I didn't draw a plan of this cabinet. I drew a rough sketch only. I determined the layout of the cutouts by placing the real parts on the top board.
Building
Woodwork
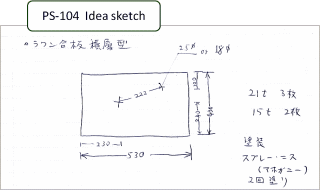
I cut two standard lauan plywood boards (15x1820x910mm and 21x1820x910mm)
to make three 21x530x430mm boards and two 15x530x430mm boards.
I made the cutouts for the parts in each board. As mentioned above, the
cutouts in the boards other than the top board were larger than the specified
dimensions. I marked out before making them referring to the rough sketch
and the real parts.
I put the bottom board on a floor, glued the next board to it with rapid
curing wood glue, put a heavy weight on it, and glued the third board when
the wood glue was half dry, and so on.
24 hours later, I sanded the front, back and side surfaces to make each
surface flush with a sander.
After applying polishing powder, I painted the cabinet with mahogany-colored
varnish spray. I sprayed only twice, though, it was finished far more beautiful
than I expected. I was very pleased. I had worried that it wouldn't be
beautiful because I didn't choose wood that has the beautiful grain. But
it was an unnecessary worry.
I forgot to take color pictures of the newly built player cabinet. I feel
sorry that I can't show you its beautiful finish.
For this woodwork, I used power tools for the first time in my life. I
used to use a hand saw to cut wooden boards and a plainer and sandpaper
glued to a piece of wood to make butt ends flush. To make holes, I used
to use a hand drill. My previous works were really handmade. It takes a
lot of time and labor to work with hand tools, and working accuracy is
not good. So I started using the power tools. I bought an electric drill.
The 'sander' mentioned above was the electric drill with a sandpaper attachment.
I borrowed a circular saw for cutting the boards.
I was really surprised by the effectiveness of the power tools. A work
that used to take several days was done for only one hour, and working
accuracy was far better. Especially, I was pleased that the front, back
and side surfaces of the cabinet were finished flush and very smooth by
sanding with the 'sander'.
Exceptionally, I made the cutouts of the turntable by using a pad saw as
I used to do. It was really troublesome to make the cutouts in the five
boards.
It took me only 7 days from purchasing the materials and finishing the above woodworking. Even though I used the power tools to improve efficiency, I think I was so powerful in my 20s. I really wish I had such will power and stamina now (August 2014) so that I can produce many excellent audio devices based on many good ideas I have in mind (sorry for grumbling).
Assembly and Adjustment
First of all, I screwed the insulator AF-10. It is fixed to the cabinet
as feet, so it's easy to place or move the player.
Next, I fixed the important parts: the turntable and the tonearm. The dimensions
of cutouts were so precise that I could fixed them without difficulty.
The following five adjustments are required before use:
- Leveling the cabinet
- The height of AF-10 is adjustable. Level the cabinet (or the turntable) by adjusting the height of AF-10. Confirm the +/- zero gradient with a spirit level.
- Adjustment of height of the tonearm's fulcrum
- Mount the cartridge on the tonearm, and lift down the stylus on the disc on the turntable. Adjust the height of the fulcrum such that the arm is parallel to the disc surface with the stylus on the disc. Confirm this by a visual check. Because G-1040 doesn't have any special mechanism to adjust the height, do it by loosening the fixing screws that fix the arm's fulcrum to the arm base (the part screwed to the cabinet to which the fulcrum is fixed), and slide up or down the arm's fulcrum. This adjustment cannot be done while the stylus is on the disc. It is necessary to repeat the adjustment and the check by turns. It is a troublesome work.
- Adjustment of the overhang
- Adjust the position of the cartridge on the headshell so that the distance between the stylus and the spindle of the turntable is 15mm when the cartridge is positioned just above the spindle.
- Adjustment of the stylus tracking force
- The tracking force is adjusted by screwing the counterweight, since G-1040 is static balanced arm. After perfectly balancing the arm (i.e. making the tracking force zero), set the calibration dial on the counterweight to zero, and screw the counterweight towards the fulcrum till the dial indicates the desired tracking force.
- Adjustment of the anti-skate mechanism
- Lift down stylus on the grooveless part of the test record, turn on the turntable to rotate at 331/3rpm, and adjust the anti-skating mechanism so that the stylus doesn't skate inward nor outward. Since G-1040's anti-skate mechanism is a simple hanging weight type unlike most hi-fi tonearms those days which used magnets, this adjustment is a little troublesome.
As soon as I finished the assembly, I installed PS-104 in the rack (the
steal rack I am still using as of August 2014), I carried out the adjustments
above. I had done them without any big trouble, but only one trouble occurred
at the last. As for it, see the next section 'My Own Review'.
PS-104 was completed on Feb. 2, 1982.
My Own Review
Comprehensive Assessment
I think I could make the player that exactly realized the concept. And,
I could do that without spending so much money.
I feel something fateful about this success. A primary factor may be that
I happened to be able to purchase the high performance/high quality parts
within my moderate budget. I was very eager to play my beloved vinyl discs
in superb sound quality forever even when the dawn of the digital era was
just around the corner. I believe my strong eagerness attracted the good
luck.
As I expected, I have been using PS-104 for many, many years. As of August
2014, it still offers better sound quality than CDs.
Turntable
The turntable TTS-8000 has no shortcoming but the mat with gel in it that
can't absorb vibration enough because it doesn't contact the entire disc.
To solve the problem, I purchased the disc stabilizer ORSONIC DS-250, which
presses the disc against the mat adequately. Whether DS-250 is used or
not affects tonal quality to a significant degree. With DS-250, PS-104
offers more clarity and less noise.
DS-250 is not a mere weight. It has a spring inside that clips the spindle
of the turntable to fix the longitudinal position of the stabilizer. That
is, the pressure to the disc is adjustable. Too strong pressure makes the
disc warp and the outer edge of the disc floating. The proper adjustment
enforces the effectiveness of the stabilizer.
TTS-8000 has a X'tal-lock switch. I tried playing a record with the switch
off (i.e. without servo control). I realized it was far better in sound
quality than X'tal-locked mode (with servo control).
The servo control makes sure that the deviation of the rotational speed
is kept within the acceptable range. On the other hand, the speed inevitably
fluctuates within the range.
The spec of TTS-8000 says its maximum wow flutter is 0.025%. The rotational
speed increases/decreases within this range. When the speed exceeds the
standard speed, the servo control makes the motor generate negative torque
and lowers the speed. When the speed decreases, the servo control makes
the motor generate positive torque and increases the speed. At every fraction
of an instant, the torque of the motor changes rapidly and largely, so
the rotation of the turntable is not smooth. And, the motor vibrates, and
the vibration reaches the turntable.
TTS-8000 has an excellent stroboscope. The 120Hz pulse train generated
by the X'tal oscillator makes the neon bulb blinks exactly at 120Hz and
illuminates the strobe markings around the edge of the turntable. It enables
you to see a slight wow flutter. I confirmed that a slight wow flutter
can be seen with the X'tal-lock on, and no wow flutter with the X'tal-lock
off. Since I realized this fact, I've been using TTS-8000 with the X'tal-lock
switch off.
It's necessary to adjust the rotational speed manually when the X'tal-lock is off, though, once it is done, the rotational speed remains unchanged for a long time. I adjust it only two or three times a year.
Tonearm
Until now (August 2014) I have been using G-1040 for more than 32 years, so I firmly believe in its reliability just like the turntable TTS-8000. However, the memo I wrote down 32 years ago lists up 10 shortcomings of this arm and says I was not satisfied with it.
The most serious problem was that one of screws which fix the tonearm's
fulcrum to the arm base was broken.This made it impossible to adjust the
height of the arm and to remove the arm's main body from the arm base.
As mention above, it was troublesome to adjust the height of the arm. So
I tighten up the screws with a pliers after the adjustment in order to
prevent an unwanted slide of the fulcrum in use. It was my mistake to use
the tool because the screws were supposed to be tightened with fingers.
But I got furious that the head of the screw came off quickly even though
I didn't use my strength so much.
Fortunately, the difference in dimension between M-14LE and F-14 was not
big, so F-14 can be used without any problem.
Another big problem was a defect of the arm lift. It was not settled at
the top position. As soon as the user got his finger off the lever, the
arm descended. And the descending speed was too fast to the extent that
the cantilever of the cartridge could be broken unless it was extremely
tough.
I contacted GRACE about this issue. I got the answer that they were going
to send me a new one after I remove the arm lift and send it to their service
department.
But I postponed the work since it was rather troublesome. Without my noticing
it, their stock of the arm lifts were run out and it became impossible
to repair it. This was resulted from my laziness and their small stock
of the spare parts of G-1040 due to its small production volume.
Whenever I play a vinyl disc, I move the lever of the arm lift slowly so
that the stylus touches down on the disc softly. I am perfectly used to
this operation, so I don't feel it's troublesome.
Cartridge
As mentioned above, I used M-14LE for a short period, and replaced it with
F-14. But I can't remember the date I did that, and don't have any memo
about this.
F-14 offered little coloration and sounded good for every genre of music,
though M-14LE excelled it in clarity. It compatibility with the tonearm
G-1040 was very good as expected. It was natural because they were products
of the same manufacturer.
I have upgraded F-14 many times thereafter such as replacing the stylus
with better one, and finally it turned to the high performance/best sounding
cartridge that was far better than I expected. For details, see the next
section 'Improvement'.
Insulator
AF-10 lived up to my expectation. But when I moved to my house where I still live, I realized the floor was not rigid enough and the amount of acoustic feedback was significant. It was necessary to improve the insulator. For this, see the next section 'Improvement'.
Improvements (before the year 2003)
I improved the cartridge and tonearm chiefly with parts I purchased directly
from GRACE which were advertised on DMs. However, I forgot when and what
part I purchased and I lost my notebook I used those days. I can't remember
the prices of each part, either.
As I can't describe each improvement in chronological order, I describe
them on part by part basis.
Tonearm Cable
I remember the tonearm cable that came with G-1040 was a so cheap one.
When I got a DM that advertised a high-grade tonearm cable that used high
quality martial such as OFC, I purchased it without hesitation. It might
have been before building PS-104 (from January 28 through February 3 in
1982) that I bought it. I bought G-1040 in November 1981 and registered
it soon. I might have got the DM before I began building PS-104. There's
possibility I used the high-grade tonearm cable from the beginning, since
I don't remember changing the tonearm cable afterwards.
Cartridge and Related Parts
Replacement stylus
I planned to change the stylus of F-14 once a year and actually I did so.
The average life of elliptical styli is about 300 hours. If you play one
LP a day, the stylus will be worn out in one year. But I didn't play a
record every day, because I was no longer a university student and didn't
have time to listen to music on week days. So the stylus was not worn out
in one year. Nevertheless, I kept changing the stylus every year for the
following two reasons:
The first reason was the aged deterioration of the suspension that supports
the cantilever. The suspension was made of rubber, and it would be aged
even though the cartridge was not used. Its life was a year or two. [2015/02/14 corrected] {This is my misunderstanding. I got e-mails from some audiophiles who visited
this website and was told the life of the suspension is much longer. I
studied this issue and got to know the life is longer than I believed.
But it is difficult to make it specific because it depends on the environmental
conditions (chiefly temperature and humidity). As for F-14, I inquired
of GRACE and waiting for the answer} I would like to maintain the highest tonal quality all the time, so I
changed the stylus every year.
The other reason was my desire to support a good analog products manufacturer
like GRACE to hand down technologies and culture concerning the vinyl record
to the younger generations. I bought many replacement styli intending the
half of the payment was donation. I kept this nearly 30 years and paid
a lot of money. It was so rare for me, who don't like to pay much money
for audio equipment. The total payment reached about 320,000 JPY as mentioned
on the top of this page. This figure is only a rough estimate.
A wide variety of replacement styli were available for F-14. At first,
I chose standard type: aluminum cantilever + elliptical stylus. I tried
some other types later.
- Elliptical stylus with aluminum cantilever
- The sound quality was very good for an MM cartridge, but it was a bit worse in clarity than M-14LE.
- Elliptical stylus with ruby cantilever
- I was rather overwhelmed when I heard its sound for the first time. It was so clear and powerful. I was keenly impressed with the fact that the cantilever influenced sound quality so much. Of course, the stylus was expensive, though, I didn't feel like buying replacement stylus units using an aluminum cantilever any more.
- Elliptical stylus with boron cantilever
- I tried out a boron cantilever that is as hard as ruby. It didn't live up to my expectation. I never bought it again.
- Microridge stylus with aluminum cantilever
- I was more overwhelmed than the ruby cantilever when I heard it for the first time. I thought F-14 was upgraded to the highest grade. F-14MR (F-14 with the microridge stylus) offered both high resolution and a remarkable spaciousness. It also gave me the feeling of being at a live performance. I felt like I could hear even the sound of the performer's breathing. Its superb sound quality was probably resulted from its high tracking ability and wide frequency range (20-55,000Hz). I had one more pleasant surprise. The old discs which I had played countless times in my teenage years and (I thought) were already worn out sounded like a virgin disc when they were played with F-14MR. Though the stylus cost more than 20,000 JPY, I used the microridge stylus only from then on.
It is a common knowledge in hi-fi circles that MC cartridges are superior
to MM cartridges. But I came to doubt it after I employed the microridge
stylus. Now I believe the shape of the stylus has more influence to sound
quality than the engine type.
The shape of the microridge stylus is almost the same as that of the cutting
machine's cutter. It traces the groove perfectly. Other stylus shapes inevitably
causes distortion. Distortion increases in the following order: microridge
==> other types of line-contact styli ==> elliptical ==> conical.
And the life of stylus decreases in the same order. The life of the microridge
is as long as 2,000 hours. The damage to the groove increases in the same
order too.
The figure below illustrates the reason for low distortion of the microridge stylus (high distortion of the conical stylus).
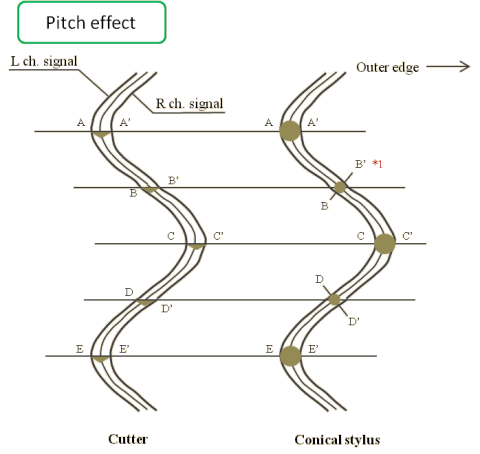
The left half of the figure illustrates a groove a cutting machine cut
and the right half shows how the conical stylus traces it. The stylus is
pushed up from the groove at the point *1 (a slanted part) and vibrates
vertically. This phenomenon is called 'pitch effect', which generates opposite
phase signal between the left and right channels. This distortion tends
to be present at narrow parts of the groove and at high frequencies.
The distance between the cutter's contact points A and B (A-B) and the
distance between A' and B' (A'-B') are the same. As for the conical stylus,
A-B will increase in length and A'-B' will decrease. This means that the
sounds of each channel will differ even if the same sound is recorded on
each channel (i.e. the signal is monaural). In short, distortion will be
produced.
This kind of distortion cannot be cancelled however the cantilever or the
engine is superb.
The shape of the microridge stylus is almost the same as the cutter. It
traces the groove as shown in the left half of the above figure. It does
not produce the distortion.
However, interestingly enough, there are still some cartridges using the
conical stylus available. Some of them, such as DENON DL-103, are highly
evaluated. Even though they produce distortion, some audiophiles like their
tonal characters. A friend of mine has been using DL-103 for many years.
He loves the cartridge and wouldn't like to replace it with another one.
DL-103 makes you feel a typical analog disc replay. It offers a kind of
sixties-style nostalgic sound. I think the distortion adds something like
sonority to the original sound.
I still regard vinyl discs as hi-fi source. I don't want the typical analog
sound. I demand low distortion and low noise even to vinyl discs. If I
find better music source, I wouldn't hesitate to employ it as Gaudi's main
source. But, so far, I haven't found anything comparable with vinyl discs.
Even if I select another source, I will never abandon my vinyl discs and
PS-104, because almost all the records I own are so special to me. I am
strongly attached to them.
The figure below illustrates how the microridge stylus traces the groove's unworn walls. This is the reason why it can replay old discs in high sound quality.
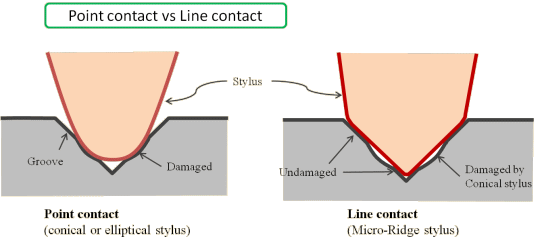
The left half of the figure illustrates how the conical or elliptical stylus will wear a part of the groove. Whereas the microridge stylus will trace the unworn parts of the groove damaged by the conical or elliptical stylus (as shown in the right half of the figure).
Headshell and headshell cable
I replaced the headshell with GRACE Carbon Fiber Headshell. At the same
time, I replaced headshell cable with GRACE LC-OFC/Silver.
Carbon Fiber Headshell is made of carbon fiber as its name suggests. It
doesn't resonate unlike metal headshells. I can't remember clearly how
much it improved sound quality compared with the original aluminum headshell
that came with G-1040, though, I think it was better than the original
one. I am still using it (as of August 2014).
LC-OFC/Silver is a set of silver-plated LC-OFC litz wires. As I employed
it the same time as the headshell, improvement in sound quality due to
this cable was not clear, either. But I guessed F-14MR offered more clarity
and better transient response thanks to this cable.
Main body of the cartridge
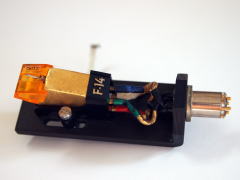
I got a DM from GRACE that advertised F-14's main body (without stylus)
that they imported back from their European agents. Though I had been told
the prototype was just the same as the product, I supposed the product
was improved version of the prototype. I purchased it.
I decided to keep the prototype as a spare cartridge, in case it becomes
a rare and expensive item in the future.
The photo on the right shows the manufactured F-14. The logotype 'F-14' is carved. It is the combination of the F-14 main body, microridge stylus, Carbon Fiber Headshell and LC-OFC/Silver cable.
Improvements (in 2003 or later)
Quitting replacing the Stylus (November 2009)
It is not improvement. I quit replacing the stylus of F-14 every year because
of a sharp rise of the price of the microridge stylus (US-14MR). It exceeded
40,000 JPY, though it had been 20,000 yen level till then. I didn't feel
it a heavy burden to change the stylus every year before the price hike,
but 40,000 yen level was too expensive for me. And other high-grade cartridges
were available for the same price range. I decided to keep using the current
stylus till it would be worn out and to purchase another high-grade cartridge
after that.
The price of US-14MR has been repeatedly risen thereafter. It is nearly
100,000 JPY now (August 2014). I am impressed that F-14 with the microridge
stylus is so attractive that there are audiophiles who want to buy the
stylus for that high price.
Improvement of the Insulator (April 2011)
When I moved to my house in May 2003, I didn't buy a new audio rack and
continued to use the steal rack I had been using since my early 20s. It
was not designed for audio use, so it had a drawback that it could be an
acoustic short-circuit. In addition to that, the living room, where Gaudi
was installed, is situated on the second floor and the floor is not rigid
enough. PS-104 received more acoustic feedback than before. Inadvertently,
however, I didn't check the acoustic feedback till 2011.
I checked it in April 2011, and realized that howling occurred at full
volume. At that time, the speaker base also had a problem and produced
more acoustic feedback. Anyway,the insulator was needed to be improved.
Insulators produced by audio products corporations are too expensive. I
looked for less expensive yet more effective one at a do-it-yourself store
and found the good one made of Hanenite Rubber. It was Tokyo Bouon THI-555,
a set of four Hanenite insulators.
I placed them under AF-10. They were so effective that the problem was
solved.
I placed them under the feet of the rack too. The acoustic feedback was
reduced furthermore.
Tokyo Bouon THI-555 | THI-555 installed |
Change of RCA Plugs (November 2011)
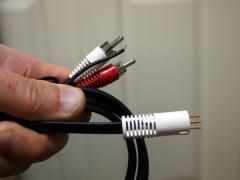
I planned to buy a new tonearm cable, because the left channel of the tonearm
cable was disconnected.
To make sure that commercially available tonearm cables could be used for
G-1040, I contacted GRACE. The answer was "No." GRACE tonearm
cables were not compatible with other makers'. Incidentally, I got a DM
that advertised that GRACE re-produced tonearm cables of which design and
materials were the same as the original ones exactly. Two types were available:
the standard and high-grade types, and their prices were 21,000 JPY and
35,000 JPY, respectively. I wouldn't like to spend much money for the cable,
so I chose the standard one.
When I looked at the cable for the first time, I was disappointed so much.
It looked very cheap no matter how you looked at it. RCA plugs were nickel-plated,
and the cable seemed to have a large stray capacity. I gave up the cable
and decided to repair the old one.
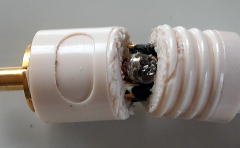
I scrutinized the broken cable and found that the solder joint of the RCA
plug was fully corroded. I have experienced the same kind of troubles several
times. Even though a product is manufactured by a first-class manufacturer,
its solder joints that are soldered by a soldering iron begin deteriorating
in 10 years and become fully corroded in 20 years. I experienced the same
thing again.
The photo on the right shows the RCA plug of the tonearm cable. The solder
was crumbled as shown.
On production lines, man hour is strictly stipulated for every work. The
standard man hour for soldering is about one second per solder joint. In
such a short time, flux cannot be burnt out and remains in the solder.
That is, the solder becomes hollow. As time goes by, the solder will corrode
from inside.
As for the technical matters, an amateur seldom excels a professional,
but soldering is one of exceptions. The professional way of soldering impairs
sound quality and shortens the life of the solder joint. I myself was an
engineer and mastered the professional soldering, but I employ my soldering
technique (I call it 'Tonochi method' lately) for every NOBODY-branded
component. (For details, see the pages of MA-201 and PA-210)
I replaced the RCA plugs of the broken tonearm cable. I used off-brand
plugs I purchased at Oyaide Denki. Though its price was as cheap as 200
JPY level, it was well-built and attractive because of its PTFE insulation.
That insulation has high heat resistance, so it is suitable for Tonochi
method.
I threw away unnecessary metal parts, because they merely impair sound
quality. After soldering, I covered the plugs with heat shrinkable tubes.
The cable was a quarter century old and the cable cores was oxidized, but
melted solder seeped into them at once and soldering was successful.
Obviously, sound quality was improved. This work can be called improvement
rather than repair. But It's not clear that the sound quality of the repaired
cable is better than when it was brand-new.
![]() |
![]() |
![]() |
New RCA plug |
It is composed of three parts. Only the main part (on right-hand side) was used | Repaired tonearm cable |
Try-out of Magnetic Levitation Insulator (January 2012)
Purchase of Yamamoto Onkyo Kogei MGB-1
I already succeeded to prevent howling by using Hanenite rubber. But I
still felt the margin was not enough. I was thinking about getting larger
margin by employing higher performance insulator.
I considered a method to prevent acoustic feedback by hanging the player
from the upper part of the rack with elasticated wires instead of putting
it on the rack board. But it seemed so difficult to realize the idea. I
gave it up and searched for good products on Internet. What I found was
Yamamoto Onkyo Kougei MGB-1. It used a pair of magnets and made the upper
magnet floating by utilizing the magnetic repulsion.
I thought it was an epoch-making invention, because I thought vibration
could never reach the upper part of the insulator from the lower part untouched
to the upper one. A set of four MGB-1s cost as expensive as 34,300 JPY,
though, I was so attracted that I bought it. It was a rare case for me,
who always claim "The more expensive an audio accessary is, the less
effective it is."
Problems of MGB-1
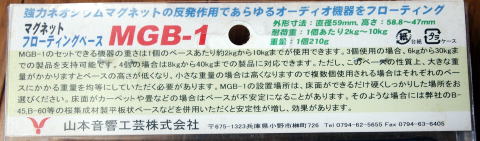
When I received this product, I noticed that the instruction manual was
not attached. The only instruction was the very simple one printed on the
package. And, it was its strong leakage flux that really surprised me.
When I put a large nail near the insulator, it was strongly attracted and
it needed a substantial force to remove the nail from the insulator.
A cartridge is so sensitive to the outer magnetic field that it will be
broken at once if it is put near MGB-1. I consulted the Service Department
of GRACE about this issue, and got an advice that I must keep a cartridge
away from MGB-1 always and I should use a cheap cartridge when I use MGB-1
for the first time to make sure of no damage to the cartridge. However,
cautions like these were not printed in the simple instruction of MGB-1.
As for the strong leakage flux, I also inquired to Yamamoto Onkyo Kougei
via e-mail. Their answer was not so concrete that it couldn't eliminate
my worry. In short, it said "Perhaps, there's no problem. Please try
it out." I e-mailed them two more times to request more concrete data
that indicated it was safe for cartridges. But they repeated the unclear
explanation. I understood from their replies that 1) they didn't have a
precise measurement instrument; 2) they didn't have know-how about measurement;
3) they didn't know the tolerance limit of cartridges concerning the outer
magnetic field; 4) they had never carried out any test using a real analog
disc player.
The following advice was included in their reply, "If you have concern
to use it for your analog disc player, why don't you use it for your amplifier?"
I was disgusted by this advice very much. The advertisement of MGB-1 said
"it is most suitable for analog disc players." They themselves
denied their claim.
Moreover, not only cartridges but many other audio devices were adversely
affected by the leakage flux. Because parts and/or wires inside an amplifier
are closer to the insulator than the cartridge of the analog disc player,
MGB-1 would rather not be suitable for amplifiers. I wondered if no engineer
who had such a basic technical knowledge worked for the company.
Magnetic shield
I couldn't give up MGB-1 as I paid much money for it, I decided to try
it out after attaching a magnetic shield to it. I can't help hearing acoustic-feedback-free
analog sound (of course, you can hear acoustic-feedback-free sound with
headphones, but I don't like headphones).
I came up with an idea that paint cans with magnetic shield sheets attached
on its inner wall would be used as a cover of MGB-1. I used Tokyo Bouon
Super Magneshield TMP-5000-II for that purpose. The manual only said its
material was a special nickel. I supposed it was almost same as Permalloy.
It was effective for both DC and AC magnetic field (unfortunately, I hear
this product was discontinued in June 2012). In addition, I wrapped the
cans with stainless steel sheet because they looked cheap.
![]() |
![]() |
![]() | |
Yamamoto Onkyo Kougei MGB-1 | Handmade magnetic shield cover | MGB-1 w/ magnetic shield cover | MGB-1 attached to the cabinet |
I tested the effect of the cover by using a compass. It was less effective
than I expected, probably because the bottom end of the cover was open.
In order to reduce the leakage flux to the cartridge as much as possible,
I glued the magnetic shield sheet to the entire bottom surface of cabinet.
I judged the leakage flux would not affect the cartridge, because the cartridge
was 14cm away from the nearest MGB-1 and the distance was enough to avoid
the bad influence of the leakage flux. I began testing MGB-1.
Review
I put a record on the turntable, lifted down the stylus on it, and turned
up the volume gradually. When the knob reached the position of 3 o'clock,
howling occurred.
I carried out one more test. With the stylus on the disc, I turned the
volume at a low level and knocked on the player cabinet with the handle
of a screw driver. A knocking noise came form the loudspeakers. Next, I
knocked on the rack board on which the player was set up in the same manner.
A similar knocking noise was heard. It means that MGB-1 did not "cut
off vibration" but let the vibration through it without reduction
at all.
I was perfectly cheated. I learned again "The more expensive an audio accessary is, the less effective it is." Looking back at its instruction on the package and the website, there was no technical data that proves its performance whereas its advertisement was so exaggerated. This kind of products are goods of poor quality and you should never buy them.
The reason why it cannot reduce vibration is that the upper magnet is not freely floating in the air but it receives strong repulsive force from the lower magnet. PS-104 weighs about 20kg. When this weight is given to the insulator, the clearance between the upper and lower magnets will be narrowed to only 2mm or so. The narrower the gap, the stronger the repulsion. This strong repulsive force propagates vibration from the lower magnet to the upper one. Only high frequencies will be reduced by MGB-1, but acoustic feedback causes the problem at relatively low frequencies. So MGB-1 is useless for preventing acoustic feedback.
Needless to say, I replaced MGB-1 with the original insulator, DENON AF-10.
New Cartridge: Ortofon 2M Red (June 2012)
The GRACE F-14, which I had been using without changing stylus since 2009, became too old and unable to reproduce trebles at last. I had a plan to buy a higher-grade cartridge some day, but I still didn't have an enough budget at that time. So I decided to buy a budget MM cartridge and to use it tentatively. What I chose was Ortofon 2M Red.
I experienced this cartridge's high sound quality through a certain FM
program.
At that time, the FM program 'Jazz Conversation' navigated by a jazz journalist
Takao Ogawa was aired in the Sunday afternoon. I was a regular listener.
In this program, Ogawa introduced high-quality vinyl records (HQ discs)
and SACDs, which were reissued famous albums.
When a certain HQ disc was aired, I felt its excellent sound quality even
through the medium like FM. I guessed a very expensive cartridge was used,
and read the homepage of the program to know what it was. It said the cartridge
was Ortofon 2M Red. I was not familiar with that. I was surprised to know
it was the cheapest one among Ortofon cartridges, when I check out the
Ortofon's website. I was attracted to this cartridge very much.
I purchased 2M Red for 9,500 JPY. I used a headshell GRACE HS-5 and a headshell
cable GRACE OFC for the cartridge. The sound quality lived up to my expectation.
I even considered it as the main cartridge of Gaudi at one time.
However, as I replayed more and more records, I became dissatisfied with
it.
It sounded vividly for some kinds of music like '50s jazz, but not for
modern recordings. I guessed this was due to its narrow frequency range
(20-20,000Hz). It didn't offer detailed and smooth sound that is characteristics
of analog records.
Its tracking ability was not enough, either. It couldn't replay Norah Jones'
record (LP, Norah Jones, Feels Like Home, Classic Records 7243 5 84800
16), which I often use for listening checks. The stylus skipped because
the width of this record's groove is narrower than ordinary LPs' and the
stylus of 2M Red was too large for the groove.
I was disappointed furthermore that old records sounded like really out-of-date
records with 2M Red. This is because 2M Red's stylus is not line-contact
type but elliptical one. This is a definitive difference between the line
contact stylus like microridge and the elliptical one. The elliptical stylus
wear the groove more than the line-contact stylus. I came to avoid playing
old records with 2M Red.
New Cartridge: Audio Technica AT33PTG/II (April 2014)
Selection
Since I began using 2M Red, I had played analog records less often, and had been considering purchasing a high-grade cartridge. I made up mind when the consumption tax hike was just around corner (April 1, 2014). I bought the new cartridge in March (just before the tax hike), and began using it in April. My selection was Audio Technica AT33PTG/II. The reasons are as follows:
- Recently designed
- There are some superb cartridges among vintage models like F-14, but I would like a contemporary one in order to replay recent HQ discs in the best sound quality.
- Hi-Fi
- It may sound like an obvious requirement, though, most cartridges have their own coloration more or less and there are few hi-fi cartridges available. I don't like coloration by the cartridge, which is the input device of the audio system. I desire the cartridge that transduces the musical information recorded in the groove into the electronic signals in high fidelity.
- Line-contact stylus
- This is the absolute requirement in my experience. For not only the high sound quality but also the long life of the stylus and less damage to records, the line-contact stylus is required. The microridge is the best.
- MC type
- I don't believe MM is inferior to MC, but in hi-fi circles, it is common knowledge that high-grade models are MC and budget models are MM. As for high-grade cartridges, you have the wider selection in MC type. And I hadn't used a low output MC cartridge, so I would like to try it once.
- Price less than 50,000 JPY
- Since I bought many audio components and parts before the tax hike, the budget for the cartridge was limited. Besides, building a hi-end audio system by using reasonable components and parts is my way of enjoying this hobby. I thought an expensive cartridge priced more than 50,000 JPY was not suitable for Gaudi.
I searched for information about reasonable MC cartridges on Internet and
found a very attractive cartridge: ZYX R50 Bloom II. Although its price
exceeded my budget, I was strongly attracted because it has the microridge
stylus and ZYX seeks not only physical hi-fi but also psychological hi-fi.
But I gave it up finally due to its high price.
I considered Ortofon Rondo Bronze too, but I passed it over because its
price didn't fall after it was discontinued and its design is old.
I searched for further information and found out that Audio Technica AT33PTG/II was sold for about 38,000 JPY at an online shopping mall. I checked out its specifications and knew excellent materials are used for it such as MicroLinear stylus (line-contact stylus), boron cantilever, neodymium magnet or PCOCC wire. The wide frequency band (15-50,000Hz) and the long life of the stylus (1,000 hours) met my requirements.The fact that it is a Japan-made product was desirable too. Consequently, I selected AT33PTG/II as the new cartridge for Gaudi.
As always, I didn't consult reviews by Japanese professional reviewers
at all for this selection. And, I selected the cartridge without auditioning.
While I don't rely on reviews by professionals, I refer to user reviews
on Internet. The user points out problems of a product straitforwardly
unlike Japanese professional reviewers, who are on the maker's side. Though
I didn't find so many reviews of AT33PTG/II, there are some interesting
ones. One of them criticized it very harshly saying, "This cartridge
is useless because the stylus is so fragile that it comes off soon."
I decided to keep this information in mind.
Installation and adjustment
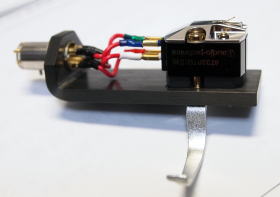
My first impression of AT33PTG/II was 'ultra precision machine.' It is of elaborate craftsmanship. Apparently, the degree of processing and assembly accuracy is higher than F-14. The tapered boron cantilever and the stylus are so small that I could hardly find the stylus with my farsighted eyes due to old age. I interpreted the harsh comment mentioned above, 'the stylus comes off soon', that this thin cantilever made of boron, which is hard yet brittle, is liable to break if you lift down the pickup speedy. I used to be careful whenever I lifted down the pickup, though, I determined to be more careful and lift down AT33PTG/II more slowly.
To install AT33PTG/II, I used GRACE Carbon Fiber Headshell and PCOCC headshell
cable that came with the cartridge.
I decided to use the MC head amplifier HA-213, which I kept in a closet
for a long time, because the RIAA equalizing stage of the preamplifier
PA-210 Simplicity is designed for MM cartridges only. As a matter of fact,
I purchased a used phono equalizer Ortofon EQA-333 for AT33PTG/II at the
same time I purchased the cartridge, because I believed HA-213 was a flop.
But for some reason, I chose HA-213 finally. For details, see the pages
of 'Gaudi in 2014' and 'HA-213' (These pages are available in my previous homepage).
I had a problem with the adjustment. The height of AT33PTG/II is lower
than that of F-14, so it was necessary to lower the height of the tonearm
to cancel the difference. But, as mentioned above, it's not possible to
adjust the height of G-1040. Though I considered to insert a lead board
between the cartridge and the headshell, I gave up the idea because I wouldn't
like to add an unwanted mass to the pickup.
In practice, the tonearm slightly slants toward the cartridge end with
the stylus on the disc, but it is not so serious and the clearance between
the body of the cartridge and the disc is wide enough. I judged the adjustment
is not necessary.
Soon after I adjusted the stylus tracking force to 2.0g, which is the recommended value by the maker, and adjusted the anti-skate mechanism, I played a vinyl record to hear its sound. At first, the output was so small. While 5 to 6 records were being played, it gradually came to sound well. After 10 records were played, the break-in was almost finished. Though I have used many cartridges before, it was my first one whose sound quality was changed so drastically by the break-in.
Listening trial
The sound quality is so good as I expected. AT33PTG/II excels F-14MR in
detail, though the latter brings a bit more space and depth into the sound.
AT33PTG/II reproduces the sound of every music instrument precisely. Voice
sounds lifelike too. I guess it is largely due to its extended high treble.
Though today's cartridges and loudspeakers tend to boost bass, AT33PTG/II's
bass response is natural. That's one of the reasons I value it highly.
AT33PTG/II lives up to my expectation in another aspect. Old records sound
like a virgin record with it. I think the MicroLinear stylus is comparable
to the microridge in tracking ability.
I have a favorite record I have played so often since the age of 14: Dave
Brubeck's 'Time Out' (LP, The Dave Brubeck Quartet, Time Out, CBS SONY
SONP 50129). Till the age of 15, I had only 5 to 6 LPs. I played them over
and over again till they were worn out. Especially, It is no exaggeration
to say that I played Time Out almost every day. I've played it often thereafter
too because it is so attractive to me. Maybe, I played it more than 500
times. It is a perfectly 'worn out' record. As with F-14MR, this 43-year-old
(as of 2014) record sound so good with AT33PTG/II.
As a matter of fact, I have two re-issued Time Out albums (SACD, SME Records
SRGS 4535; LP, Jazz Wax Records JWR 4525). But both were not as good as
the old one. Bass is unnaturally boosted and sound like it is specially
featured. On the other hand, the sound of the cymbal is less energetic
and sounds too reserved. The side-B's first track 'Three to Get Ready'
is the good example to explain it. I still love the oldest one most and
will play it when I'd like to listen to Time Out in the future.
I am satisfied with AT33PTG/II 100%, but at the same time, I understand
why it is not as popular as AT33EV in the same product line. Audiophiles
who are seeking pure analog sound or regarding a character of each cartridge
as important thing and select the best cartridge according to his/her mood
or the genre of music may not be fully satisfied with AT33PTG/II. Surely,
the sound quality of AT33PTG/II is superb, but sometimes I feel its sound
is too neutral like listening to a hi-res music file.
But it is the one I have desired. I want to use it as long as it works.
I have been supporting GRACE for many years. Now I also would like to support Audio-Technica and wish they pass their excellent audio technologies onto the next generation and develop further breakthroughs.
[2015/02/01 added[ {
I have replayed many records of various kinds of music and various kinds
of musical instruments, and confirmed that AT33PTG/II can reproduce any
kind of musical instrument's sound precisely.
The most difficult record for a cartridge to trace in my collection is
Herbie Mann's direct-to-disc-recording LP (Herbie Mann, Forest Rain, Herbie
Mann Music HMM-1). This album features Herbie Mann's flute performance
and the sound of flute is the most difficult to reproduce with an analog
record. Moreover, its cutting level and the peak level are so high that
even F-14MR couldn't trace this record and its stylus skipped sometimes
(its groove pitch is about 0.12mm and the recording time per side is 15
minutes). Of course, 2M Red can't either.
AT33PTG/II can trace the record without problem. This proves that the tracking
ability of AT33PTG/II is higher than F-14MR. I have believed for many years
that MM type tends to have higher tracking ability than MC type, so I was
a little surprised. I think AT33PTG/II's high tracking ability is resulted
from the advanced technology developed for the past 30 years.
This fact also implies that AT33PTG/II and G-1040 are well-matched. G-1040
doesn't have a good compatibility with light tracking force cartridges.
When I used F-14MR,I adjusted the tracking force to 2.0g, higher than the recommended value
of 1.8g[2015/02/14 corrected] {I adjusted the tracking force to 1.8g, greater than the recommended value
of 1.5g}. I use AT33PTG/II with its recommended tracking force of 2.0g when the ambient
temperature is 20-23 degrees C. That tracking force is the best for G-1040
too.
I conducted one more test. I digitally recorded some of my audiophile LPs by using AT33PTG/II and the digital recorder KORG MR-2000S. The format was DSD 5.6M (DIFF). The result was that the recordings sounded better than the real-time record replay. This is probably because the adverse affect of acoustic feedback was got rid of (the power amplifiers were off during the recording). And, incredibly, the recordings sounded better than downloaded hi-res music files too!!! I suppose this resulted from AT33PTG/II's excellent sound quality characterized by low distortion and little coloration. I'd like to write detailed information about this in another page later.
Those experiences made me think AT33PTG/II is my best sounding cartridge
I have heard. It is the first time in ages as F-14MR has been my best sounding
cartridge for more than 30 years.
}
Other comments
I had a pleasant surprise. It was the head amplifier HA-213. It is not a well-designed but makeshift amplifier, which I originally designed as a headphone amplifier. Although the circuit design was already finished, I re-designed it as an MC head amplifier for it became necessary due to aged deterioration of F-14MR. I believed it was an utter failure (for further details, see the page 'HA-213'). However, Its sound quality is far better than I expected.
This is just an aside. I found a user review on Internet that said it took more than one year to break in AT33PTG/II and its sound might change further. I guess this tonal change is not due to break-in but due to temperature change. The optimum tracking force changes with temperature. While MM cartridges are not affected so much by a small difference of tracking force from the optimum value, MCs are affected significantly. So it is necessary to adjust the tracking force on season by season basis. I guess the reviewer keeps the same tracking force regardless of temperature.
Summing Up
As of September 2014, the configuration of PS-104 is as shown below. I
think it is completed just as I have desired for many years. I want to
use it on a permanent basis in this configuration.
[2022/05/27 added] {I replaced PS-104 with Pioneer PLX-1000 in June 2017. Then, Technics SL-1200GR
replaced it in July 2017. AT33PTG/II is still in use with SL-1200GR}
Category | Manufacturer | Model No. | List price (w/o tax) | Purchase price (w/ tax) | Note |
---|---|---|---|---|---|
Turntable | Sony | TTS-8000 | 80,000 JPY | 19,800 JPY | Used w/ X'tal-lock off |
Tonearm | Grace | G-1040 | 28,000 JPY | 16,000 JPY | |
Tonearm cable | Grace | OFC low-capacitance cable | (Unknown) | (Unknown) | RCA plugs repalced |
Cartridge | audio-technica | AT33PTG/II | 58,000 JPY | 38,300 JPY | |
Headshell | Grace | Carbon fiber | (Unknown) | (>10,000 JPY) | |
Headshell cable | audio-technica | PCOCC cable | - | - | Accessory of AT33PTG/II |
Cabinet | (DIY) | Layered plywood type | - | - | |
Insulator | DENON Tokyo Bouon |
AF-10 THI-555 |
5,000 JPY 1,940 JPY |
(Unknown) 1,600 JPY (?) |
|
Disc stabilizer | ORSONIC | DS-250 | (Unknown) | (Unknown) | |
Record cleaner | Maxell | AE-320 | (Unknown) | (Unknown) | Powered type |
Stylus cleaner | (Unknown) | (Unknown) | (Unknown) | (Unknown) | Carbon fiber brush |